CELEBRATING OUR ACHIEVEMENTS
Our hardworking teams of log crews, truckers, mechanics/technicians, office staff, and management personal have not only moved the needle for Parnell Inc. but for the logging industry as a whole. We are proud to share the awards we have received for our dedication below.
Timber Harvesting:
2008 Logging Business of the Year
Each year, after thorough interviews and inspection Timber Harvesting & Wood Fiber Operations magazine awards one team the title "Logging Business of the Year". Given the vast number of well managed logging groups in the United State's and Timber Harvesting's firm application criteria it is needless to say that this acknowledgement means a great deal to each of our crew members and staff.
​
Below is a transcription of "Growing Better: Parnell Inc. of Alabama is Timber Harvesting's 2008 Logging Business of the Year." by Rich Donnell featuring photos by Bryan Carter.

MAPLESVILLE, ALA.
Parnell Inc., led by James Parnell and his three sons - Jimmy, Jeff and Joseph (current operations manager) - is Timber Harvesting's 2008 Logging Business of the Year. The family principals have continued to grow and diversify their business during this decade by never taking their collective eye off the ball, despite the dramatic economic downturn of the past two years. They pay excruciating attention to production and operations data and costs. They keep their finger on the pulse of market trends and opportunities, and react quickly to them. They are sincerely devoted to the health of the logging profession as exemplified by their participation and leadership in organizations that address the critical issues of the day.
And the Parnell family proceeds with a Christian humbleness through the good times and the bad.
One other thing: the Parnells are still pretty good at relying on gut feeling, a skill perfected and passed along by James, who started his own crew when he was 16 years old in 1960, in the days of mule teams, bobtail trucks, chainsaws and, well, gut feeling.
Parnell Inc. is the first Alabama firm to be selected for the award and the 11th so honored since the magazine began the recognition in 1998. As usual, the award will be presented at the American Loggers Council annual meeting, this year set for September 25th to 27th in Montgomery, Ala. Parnell Inc. was the 2006 Alabama Logger of the Year, was also judged the South Central Region's 2006 Outstanding Logger by the Forest Resource Assn. and was one of five finalists in that group's 2007 National Outstanding Logger competition.
Through the years James, aided by his wife, Sandra, built an excellent reputation and a successful logging operation and timber dealership. The former Hammermill Paper Co. mill in Selma, Ala. (eventually purchased by International Paper) became one of his primary markets.
The sons began working in the woods at an early age and gradually inherited management responsibilities as they completed their schooling. (Jimmy and Joseph graduated from Auburn University and the University of Alabama, respectively.)
​
​
​
​
​
​
​
​
​
​
​
​
​
​
- GROWTH, CURVES
As the business entered this decade, who could have guessed that Parnell Inc. would expand from one crew to five (two clear-cut crews, two thinning crews and a fuel chipping job), and that its production would explode to 465,000 thousand tons annually (estimated for 2008). In fact, over the past five years its investment growth was nearly 400%.
It hasn't come without some severe curves in the road not unlike those that punctuate U.S. highway 82 leading to Maplesville and central Alabama. Even as the Alabama Forestry Assn. was naming Parnell Inc. its Logger of the Year in 2006, the home building boom was slowing at the same time every logger's cost of fuel, parts, tires and other consumables was skyrocketing.
The Parnells became caught in a bind. The company's modus operandi for many years had been - in the fourth quarter and following the first quarter - to stockpile up a year's worth of standing timber (timber deeds) purchased from private landowners through a contractual agreement with a given amount of time to harvest, and to subsequently lock in sawlog rates with the mills from those tracts, which usually helped to define logging costs, barring the unexpected. But in 2007, their logging costs doubled, interest rates rose, and Parnell Inc. took a beating on those tracts, though the mills honored the locked in prices. “We weren't prepared for it,“ Jimmy says. “We had been buying our timber like that for 20 years. We had never seen logging costs change like that.”
Joseph adds, “We learned that we couldn't own that much inventory in the future, that we couldn’t have that kind of exposure.”
Pulpwood prices were not under contract and the business took a considerable loss on that portion of its inventory due to the price cuts during a severe drought.
Late in 2007 Parnell Inc. put plans into action attempting to prevent 2008 from being as difficult as 2007 and focusing on becoming more efficient. “With a considerable amount of prayer, our plans have worked so far this year,” Joseph says.
Foremost was changing their procurement strategy to better complement market conditions.
For the first time in the company's history, the Parnells went to each employee to discuss the company's financial situation and asked employees to help in cutting costs. They discussed ways to save on fuel and other consumables.
They also asked employees to share a portion of healthcare costs. Until February 2008, Parnell Inc. had covered all employee health insurance. Finally, the Parnells used the downturn as an opportunity to let some of their least productive workers go.
Another aspect of the business where the Parnells have tightened up is record keeping. Not that they didn't maintain accurate and updated records, but as Joseph says, with only slight exaggeration, it was “out of boxes in the back of our pickups.” Joseph also worked from an office in his house, along with his wife, Jodi, but they were having to do the paperwork at nights and on weekends and it became overwhelming and time-consuming.
The Parnells for many years had owned a piece of farm property with a rental house on it and they promptly remodeled the house into a business office while at the same time converting a hay barn on site into a truck shop.
They recruited an office manager, Tammy Smith Soltishick, whom they had No no locally for years and who had grown up around the timber business.
This has allowed the family principals to focus even more on the daily efficiencies of their operation, ever so crucial as their fuel bill increased 100% from December 2007 to June 2008 and became the number one expense of the business for the first time ever. “The fact that we've made it through the first eight months of this year, we ought to be running around crowing,” Jimmy says.
No one likes to hear about loggers going out of business, but the Parnells recognize that in today's tight economy there is opportunity in survival, or at least relief for whoever is left. “It looks like you're going to have to be big time or little time,” James says, Referring to the size of logging operations and acknowledging that well the nimble contractor with a truck and a chainsaw will always have a place, the going could be more difficult for the small to medium sized traditional contractor.
​
- MARKET SHIFT
Another major development for the family occurred in late 2006 when Parnell's longtime market, International Paper, sold its timberland in the region to institutional investors who tabbed Resource Management Service (RMS) to manage it. Parnell Inc does contract work for RMS and in some cases is hired to cut and market RMS timber. RMS maintains fiber agreements with IP as part of the transaction.
“They’re Maximizing their stumpage, where previously IP tried to log the mill,” Joseph says.
“Before, we were doing basically log and pulpwood sorts. Now we have big log and little log sorts, poles, canter wood, pulpwood, hardwood logs - a lot more merchandising,” Jeff adds. (Parnell Inc. had already been doing this with its own stumpage.)
The parnells described their relationship with RMS as “lock and key.” “They gave us the maps, we locate the timber, harvest it, chip it, performed BMP work and it's ready for the them to turn over to their site prep people,” Jeff says.
James notes gladly that when RMS foresters say they're going to be in the woods at 7 a.m., “they’re in the woods; they’re on the job. I like that.”
“They’re good people too,” Joseph says. “When they tell you something, they mean it. They aren’t fussing and cussing. They talk to you man to man.”
The Parnells usually work within a 60 mile radius of the office. Five years ago 90% of the company's production was from stumpage they had purchased from land owners, but as the operation has grown that figure has declined to about a third of production.
At least 70% of production is sawlog material (including chip-n-saw), with most sawlogs bound for West Fraser Timber's mill in Maplesville. Pulpwood is moved to IP pulp mills at Prattville, Selma and Pine Hill (formerly Weyeshaeuser).
With regard to IP, Joseph says the company is perceived as the “big bad wolf” by many. He says it's an unfair perception. “They understand what this industry is facing and they have tried to be an agent of change, and a lot of times they have pushed these changes on loggers to make this a viable industry,” he says.
Another increasingly sticky issue for the Parnells, because of the reduction in logging capacity in the area, is balancing demand from sawmills and pulp mills and potentially wood energy facilities. This has become even tougher as land owners hold on to grade timber during a depressed market.
- BIG TIME
At age 64, James still overseas Crew 1, which performs final harvests of natural growth stands and plantations. James runs a Tigercat T250 track loader. The job also includes a Tigercat 860D with a Waratah 624 processor, Tigercat 724E feller-bunched, and Tigercat 630C and John Deere 748GIII skidders.
Crew 2 started up in 2003 and is headed by Jeff, 40, who also operates a Tigercat T250 track loader. Other equipment includes a Tigercat 724D feller-buncher, and Tigercat 625 six wheel and John Deere 748GIII skidders. This crew clear-cuts and works exclusively in final harvest pine plantations.
But what makes Crew 2 unique is that it operates multi-shifts, and has been doing so for more than three years. “Everybody else seemed to quit multi shifts, and everybody thought we would, but it's been too good to us,” says Joseph, 35. (He and Jimmy, 43, manage the business side of the company.)
Jeff adds, “You get in there in the morning and you have 8-20 loads processed and ready to go; you can get your day started quick.”
Crew 2, and also Crew 1 at times, implements roadside processing, sorting and loading, which maximizes equipment and wood flow.
The multi-shift also enables the operation to utilize its trucks more efficiently. Jonathan Calloway is the night crew foreman, operating the Tigercat 822 with Waratah 622B processing head.
Crew 3 three came up and running in 2004 and specializes in first and second thinnings. Steve Lazar is the foreman and operates at Tigercat 720 f-b. The job also runs a Prentice 384 loader and Tigercat 610 skidder, as well as a Chambers DeLimbinator.
​
​
​
​
​
​
​​
​
​
Crew 4 was established in 2005 and is led by William Green. It initially performed final harvests on tracts that were too small for the large clear-cut crews, but today first-thins about 75% of the time. Equipment includes a Prentice 384 loader, John Deere 843 f-b, two JD 648 f-b, two JD 648GIII skidders and another Chambers DeLimbinator.
Crew 5 started up in 2006 and provides boiler fuel chips to pulp mills. Led by Tommy Smitherman, it operates a more Morbark 50/48 drum chipper and two John Deere 648GIII skidders. This crew also pre-commercial thins with a feller-buncher.
Other machinery that floats throughout the crews includes a Tigercat 860D track unit with Deharco stroke delimber and a Timberjwck 608S with Waratah 622 processor. Equipment runs with Firestone tires.
​
​
​
​
​
​
​
​
​
​
​
​
​
​
​
​
​
​
​
- CHIPPING START
The fuel chips crew is indicative of the diversification and opportunity Parnell Inc. continues to seek out. “We believe biofuels and biomass are the future of our industry,” Joseph says. “We think it could become our primary market.”
The Parnells point to numerous energy/fuel plants that have either just started up or are on the drawing board that would rely on low quality wood fiber. This is the first time the Parnells have ever gone into chipping.
Prior to going to the drum style chipper, the Parnells looked at horizontal grinders, but they didn't produce the kind of material desired by IP mills at Prattville and Selma, which have fuel handling systems geared to chips. The Parnells also looked at a conventional knife chipper but ran into feeding issues, since they wanted to primarily put in tops and limbs as opposed to longer stems.
Joseph found the chipper they operate - a used machine with 900 hours - online in the state of Washington. He flew out and watched it run, purchased it through a broker and had it transported to Alabama. Changes to it had to be made, however.
The chipper was set up to rear load and the Parnells purchased some closed top trailers. But the chipper blower didn't have the velocity like a clean chipper, and while it could fully load the trailer, a ways down the road material would shake down, leaving two to three feet of space in a van. They were averaging just over 20 tons per load of mostly drier material.
They modified the chipper to load from the top with a chute, so that trucks with open top trailers can drive under it, and it now throws chips down about 8 ft. at the same velocity it was throwing 40 ft. before. The 40 ft. open top trailer gained at least 25% weight in the same material compared to the closed top. They also began skipping tracks and staying right behind the logging crew for the less dry material. Then they purchased some possum belly trailers and today can load 29 tons, with the trailers only three quarters full.
​
​
​
​
​
​
​
​
​
​
It took a year of getting skidder operators acclimated to picking up tops and leaving them near the decking area instead of moving them away from the landing and spreading them on the ground. And "picking up" truly means picking them up with the grapple to lessen dirt contamination.
The chipping job averages eight loads per day, but has the capacity to do 20. It has loaded two trailers in 30 minutes. The chip produced is about a 3/4 in. square, smaller than a conventional chip.
“There’s a tremendous amount of waste out there that could be used, but it’s not being used,” James comments.
That reality hit home when they demoed a horizontal grinder on a 40 acre block of mostly hardwood that they thought they had logged "clean", moving out more than 100 loads of pulpwood and logs. But they chipped another 30% of material granted hardwood has more tops, but they're still averaging 18-19% behind pine.
In addition to the IP mills at Selma and Prattville, Parnell Inc. delivers chips to the IP mill at Pine Hill. James is especially impressed with Pine Hill's quickness at unloading the fuel trucks, simply using a dump for trucks to back up on and unload onto a pad, followed by a loader that pushes material away. Unloading time averages 10 minutes.
- UTILIZATION
Most equipment is purchased from Warrior Tractor and Equipment (John Deere, Waratah) in Northport and G&S Equipment (Tigercat) in Prattville. James has good thing to say about both operations, and he likes to see them competing for his business. Parnell Inc.'s equipment preference has steered toward Tigercat in recent years because of its “excellent uptime.”
The most recent machinery purchases, since 2006, were the 720 and 724 feller-bunchers, 860 track machine, 610 skidder and a 624 processing head.
With regard to productive machine time, Parnell Inc. is in the process of re-committing itself to the use of Multi-Dat Data Loggers with GPS in its machinery. This involves internal motion sensors to detect machine vibration, with machine operators entering various codes as to why the machine isn't operating, such as “out of wood” or “no truck” or “fuel service.” Parnell ran them for two years but got away from them because of the amount of time it took to maintain and analyze the data. However, the recorders produced eye opening results. The Parnells thought they were operating at least 80% uptime, but the data revealed in the low 50 percentile.
The goal is 80% utilization, taking into consideration brakes, lunch, fuel and service.
Now that they have an office manager, the Parnells intend for her to organize the data and maintain graphs and trends, so that each week they can have tailgate meetings with the crews to go over the info. It will enable operators to see how much they compare with each other, creating productive competition, and could reveal operational bottlenecks.
In addition to machine uptime, machine hours are receiving greater emphasis, as in more of them - as in shooting for the 25,000 hour range on some equipment.
“In the 50 Years I've been in business the only times I've made a profit or accumulated anything was after equipment was paid for,” James says. “You take care of it and then you run it as long as you can.”
Two days equipment does cost much more but it is also much better designed and fabricated, meaning it lasts longer. “We hear about people getting 20,000 hours or even more in places like South America; it can happen here,” James adds.
Heat has always been an excuse for lower machine life in the South, but a group of Brazilians visited the Parnells a couple of years ago and revealed that their machines had run up 30,000 productive hours.
The Parnells operated in 1999 tiger cat 860 with a stroke delimber with 18,000 hours on it. The machine has never had a service call, they say. Some other machinery is accumulating the hours as well. The Parnells go by the book and keep the detailed maintenance records. Well-equipped service trucks attend to each crew. It would help, James says, if the machines operated in the deep South had tropical type cooling packages. “We’re tropical in the summer, there’s no doubt about it,” he emphasizes.
- TRUCKING
Parnell Inc. runs 19 Peterbilt trucks and one Kenworth, pulling 17 Pitts log trailers and two made by Magnolia. They also have three ITI open top chip vans, two Peerless vans and three lowboys. It contracts with a handful of truckers.
The newest trucks are 2006 models and the oldest goes back to 1995. The Parnells plan on running them over a million miles, and on average they currently have 400,000-450,000 miles on them. A very intensive maintenance program features two full-time mechanics.
Right now, through southern LINC radios and GPS, truck routes are determined through constant communication between family principles, foremen and drivers. A dispatcher is being considered.
All trucks are fitted with SI scales. “We lost way more money trying to be legal without scales, than what the scales cost,” James says. In addition, Jeff adds, “The drivers tell me it's nice to leave the woods and know their trucks are legal weight. There's so much less stress.”
Earlier this decade, the company experimented with central tire inflation systems. This led to the installation of five sets. CTI units help maintain an increased production by giving trucking a larger operating window. CTI-equipped trucks can go in wet weather, can cross sensitive fields, or help heal a road for other trucks not so equipped. They also minimize time and costs associated with pulling stalled trucks to public roads.
The company has hired a retired state trooper as a consultant on DOT issues, specifications and paperwork.
The Parnells estimate that at least 60% of log trucks in their operating area are grossly overweight. But they can't afford to worry about other rigs. Large trucking operations like theirs have become fair liability game, and a slip-up can wreak havoc on the business.
The Parnells have been talking about going to a lighter weight truck. “It's just hard to figure out how you can afford something brand new when what you have is working,” Jimmy says.
Joseph agrees, but smiles at the thought of gaining nearly two tons per load and a mile per gallon, which is basically 20% more fuel economy. “But do you want to get $2 million in debt?” he asks. “It’ll pay for itself if you can continue to work, but what if you have to cut back 50%?”
- EMPLOYMENT
Parnell Inc. employs 53. The company claims to pay better than most, including a base hourly rate, overtime and crew production incentives, but the Parnells demand 100% from their workers. They maintain a profit-sharing program enacted in the '80s and they now pay half of health and dental insurance of their workers.
They also require drug testing upon hiring and do random testing thereafter. “This gives us a higher quality of person,” Joseph says. “Predictable, better people.”
Still they shake their heads at the number of potential hires who don't show up for the initial drug test.
Employees are certified in CPR and first aid, and monthly safety meetings review issues and procedures. CB radios in all equipment enhance safety communication.
They've had one workers' comp claim in more than 20 years, and it surfaced following a fight between two employees as opposed to a woods accident.
The Parnells are genuinely concerned about the livelihood of their employees, which relates to the stability of their company and to the health of the logging industry as a whole.
“I would like to see us be paid enough that we're comfortable and in return be able to offer a better life to our employees,” Joseph says. “We need enough margin to offer our employees a better life.”
The Parnells recognize that no other industry in the country would operate with the margins that the logging industry operates on. Their collective comment: “With the investment we have, we shouldn’t be ashamed of making money.”
They also recognize that the overall dwindling of the logging ranks was brought on by various factors, including a general economic upheaval. While painful to observe, this development possesses an opportunity for Parnell Inc. to improve its situation.
The multiple crews and diversity of Parnell Inc. surely gives it an advantage. “One thing different about us,” Jimmy states, “when a mill asks if we can do something, we don’t tell them no. We’ll try to figure out a way to do it. That has kept us on the cutting edge.”
There is even talk of adding a sixth crew - another thinning crew similar to the current thinning jobs. The Parnells are Hesitant to make the investment given the current conditions, but they see a demand for more quality thinning capacity.
​
- PROACTIVE
The Parnells do all they can on their job sites and with their trucks to present an environmentally aware, professional operation. They've also stepped out of their own backyard so-to-speak to bring their leadership to industry groups. Joseph is on the board of directors of the Forest Resource Association and is co-chairman of the FRA National Wood Fiber Supply Chain Committee. He's also on the board of the Wood Supply Research Institute and is a member of its technical committee.
Joseph also participates in the Forestry Lead Use Group (FLUG) with John Deere, working with engineers to determine what changes are needed and remain competitive.
Jimmy serves on the board of the Alabama Forest Fund, which is the workers' comp self-insurance organization of the Alabama Forestry Assn.
Jimmy also overseas and has been instrumental in expanding, Parnell Inc.'s cattle division, which day encompasses 700 head of brood cows and a 2,500 head stocker cattle operation. Jimm is running for president of the Alabama Farmers Federation, for which he currently serves as a district director, and he is on the board of the Chilton County Farmers Federation and is a member of the Federation's State Forestry Committee. He has long be active in Chilton County politics including a stint as Republican party Chairman.
Parnell Inc. is a member of the Alabama Forestry Assn. Joseph comments, “We all need to support these loggers' councils and associations that can put people in place to make the lawmakers understand what we're facing, especially with issues like weight restrictions on federal highways and tax relief on fuel. We've got to keep people like Bill Jones (director of the Alabama Loggers Council of AFA) in place. When we have an issue with somebody like DOT, Bill will get in the car and go talk to those guys.”
Joseph also emphasizes the importance of loggers working together, even to the point of pooling trucks and possibly woods equipment, although his dad James, questions whether the independent nature of most loggers will invite such cooperation.
What James is looking for in his business these days is simply “relief.”
“We are operating on too short of a string,” he says.
The stress trickles down to the crew as well and James recalls a recent day in the woods when everybody was griping about everything with none of it having any real substance.
“I Had a little meeting and I told them I didn't want to hear a bad thing said about nobody or anything for the rest of the day; that I didn't want anything but a good conversation.”
The crew recognized that their boss was exactly right and then quickly heeded his instructions. The remainder of the day they were as productive as they had ever been.



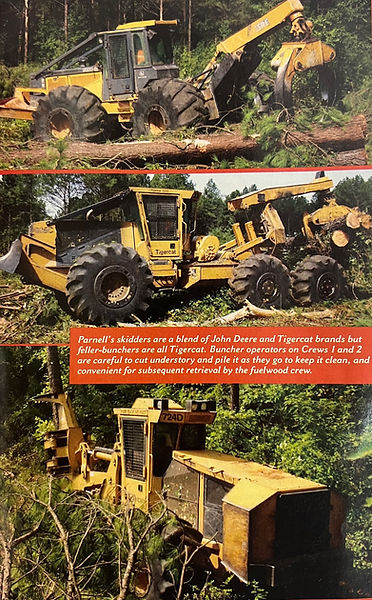